Injection molding
Injection molding is suitable for the manufacture of both small series and large series. It is a so-called forming process. The accuracy of the injection-molded parts produced is what makes it so popular. For example, the automotive sector has very high standards of quality - meaning that processing needs to have a high level of accuracy.
With our machine park of 11 injection molding machines, we offer precise components for further processing at your company.

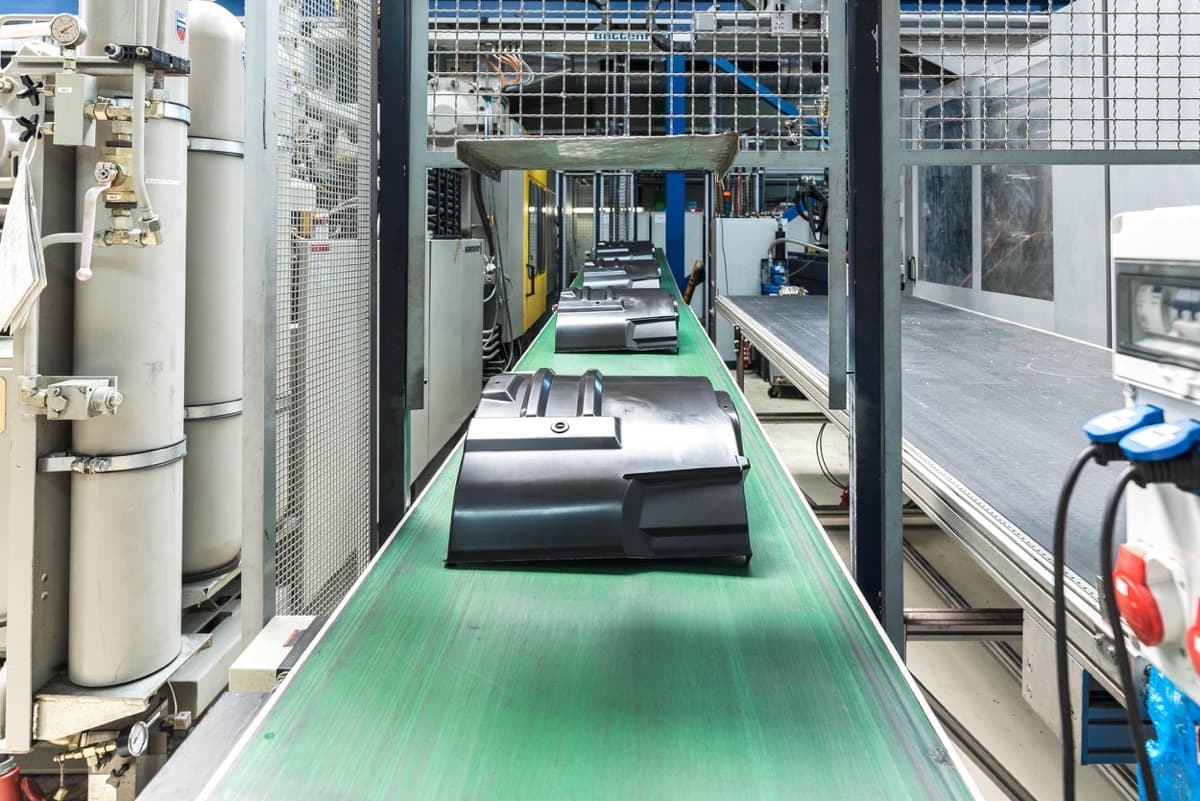

One special feature is our injection molded parts with thick walls and large surface areas. This involves plastic being liquefied in an injection molding machine before being injected into a steel injection molding form. The application of pressure compensates the shrinkage of the plastic (resulting from cooling) by adding further plastic. When cooled the mold becomes rigid again and maintains its form. The tool is opened and the plastic part can be removed.
This is an individual process for each plastic part, comprising temperature, pressure, time, material and tool-specific parameters.
Advantages of injection molding:
- 11 injection molding machines (75t to 3,200 t clamping force)
- Each machine is equipped with a removal robot
- Shot/part weights of 20 g to 40 kg
- Characteristic: injection molded parts with thick walls and large surface areas
- We process all technical thermoplastics
- Manufacture of technical plastic parts for interior / exterior use
- Components for small series, medium-sized series and after-series supply
- High reproduction accuracy in the manufacturing process
- No or little post-processing of the molded part required
- Direct route from raw material to finished part
- Procedure can be fully automated
- Depending on the part, very high volumes can be manufactured per hour