Your specialist for rotational sintering
With extensive experience in plastic processing, we use the rotational smelting procedure to manufacture complex plastic hollow parts of any shape and size from thermoplastic material, according to your individual specifications. We are able to support you with your idea from the design onwards. To begin with there is a planning phase, in which we join you in developing the best-possible realization for your desired product. Take advantage of our many years of experience and leave the production of your plastic parts to us.
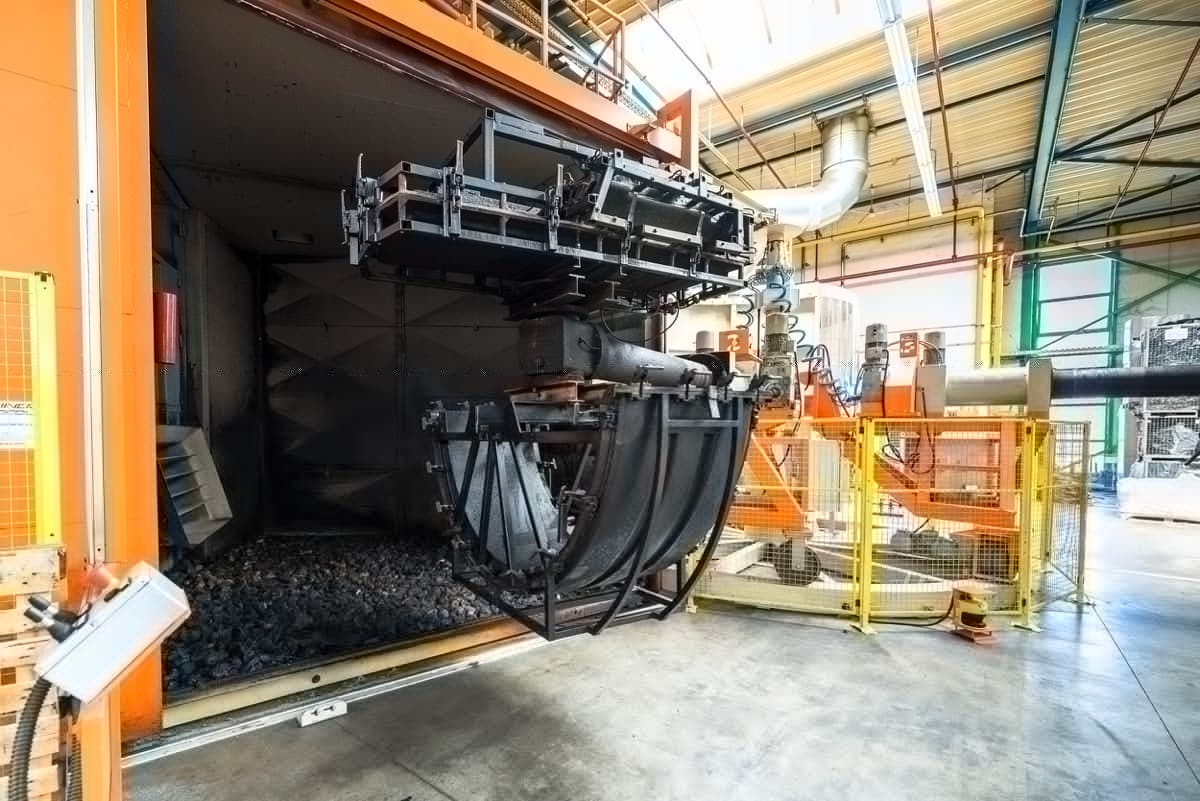

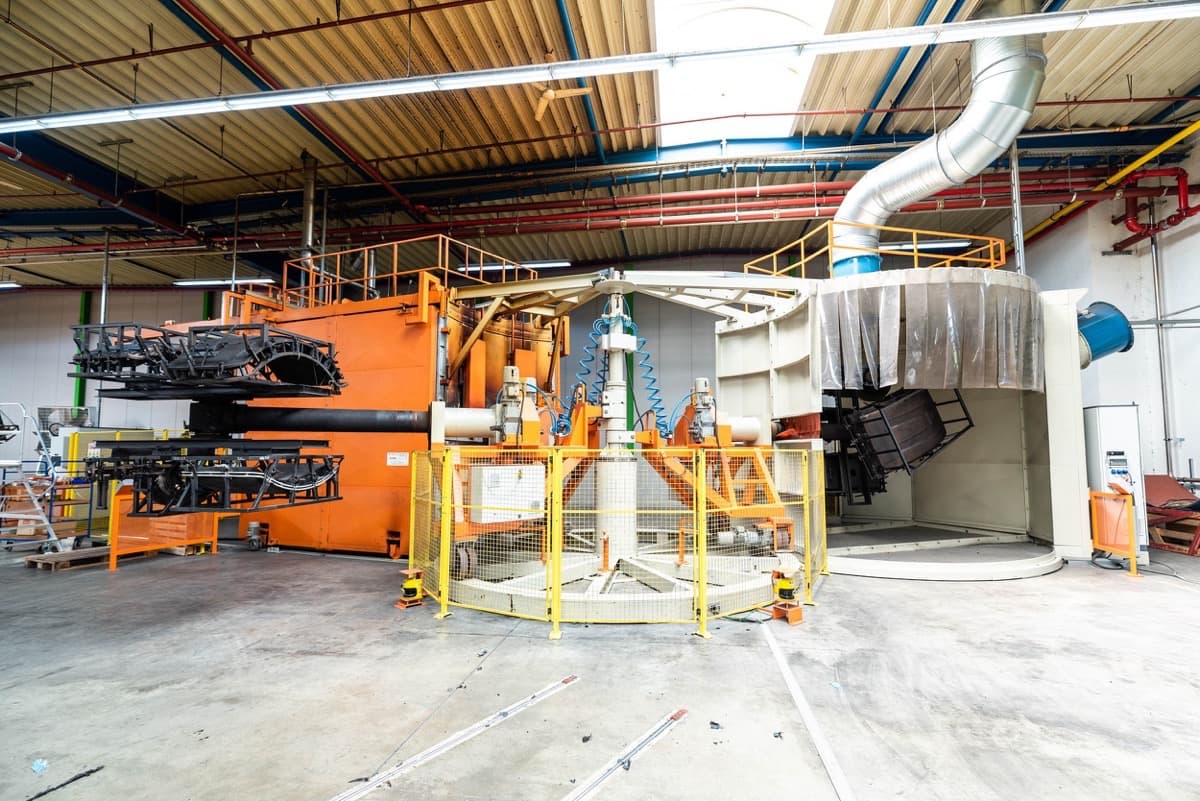
Rotation units for even higher performance
The history of Henry Technologies GmbH dates back to the early 1970s. In 2015 the new 3-arm rotation unit with a 3.50 m carousel machine was installed. This expansion of our existing machine park in the field of rotational and injection molding opens up the means for even higher performance. In 2018, installation of a second rotation machine, 4.7-meter carousel machine with 2 straight arms and 1 L-shaped arm.
/ | Roto 1 (2015) | Roto 2 (2018) |
---|---|---|
max. volume Rotary kiln | 22,5 m³ | 61,5 m ³ |
Wall thickness | 2 mm – 10 mm | 2 mm – 10 mm |
max. Tool weight | 0,95 t | 1,3t / 2,5t |
theo. max. WZ-Volume | 10 m³ | 30 m³ / 35 m³ |
Rotational molding process
Rotational molding is a rotational process in which plastic is processed without pressure.
During rotational sintering we use plastic powder with thermoplastic properties. Powder material is added to the hollow forms, before rotational arm and rotary plate begin to slowly rotate the mold. The rotational mold filled with the powder material is moved biaxially in the smelting furnace chamber at around 300° C.
During controlled warming the material melts slowly, adhering gradually to the interior wall of the mold and building up the wall thickness of the plastic part in layers. After this, ventilators circulate cool air around the plastic parts still located in the tool. During the cooling phase rotation continues to ensure that the plastic maintains its desired form as it solidifies. After controlled cooling the finished plastic part is removed.
Advantages:
- max. volumes of 46 m³
- Wall thicknesses of approx. 2 mm to 10 mm
- The hollow parts and containers can be rotated in one piece without other connections
- Completed molded parts are almost stress and tension-free and resistant to impacts and pressure
- Production of single-walled, double-walled and multiple-layers molded parts as controllable parameter
- Manufacture of large volume parts
- Low tool costs = improved economy for small quantities
- Material types: PE is standard material, other materials on request
- Standard colors: all RAL individually applicable